コスト削減!
3S活動
徹底した3S活動で、業務の効率化を図っています!
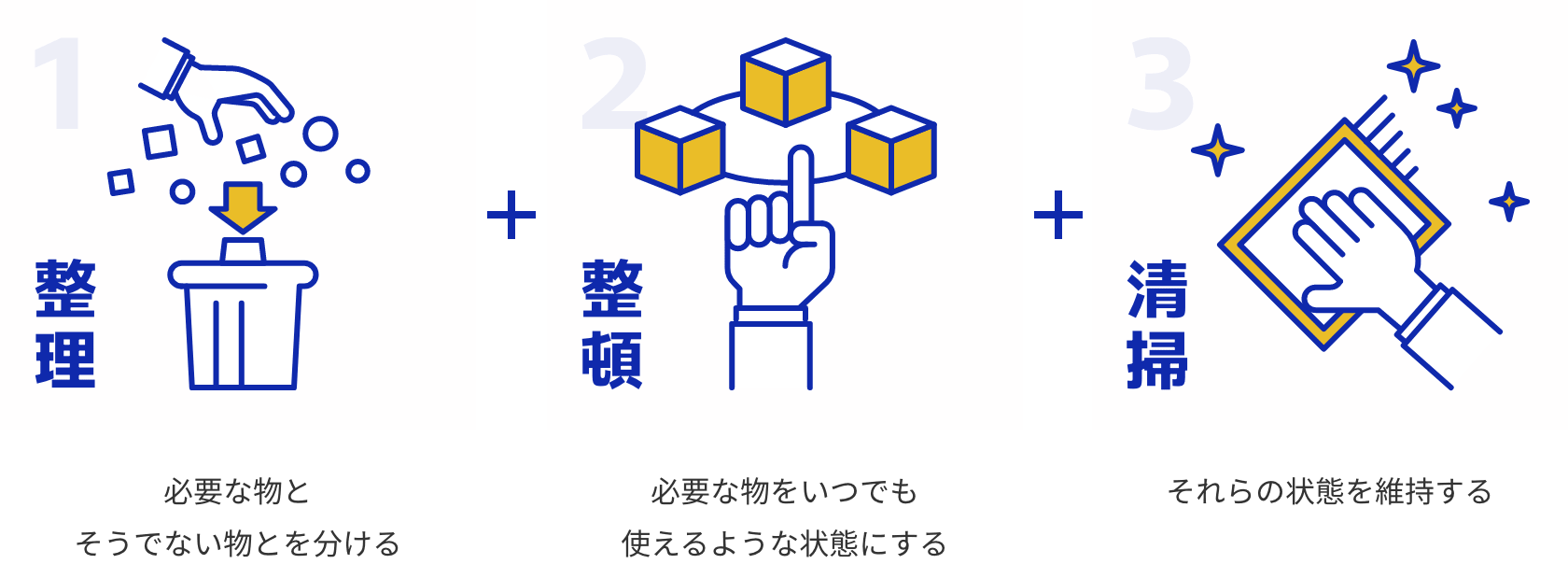
3S活動の「見える化」がもたらした効果
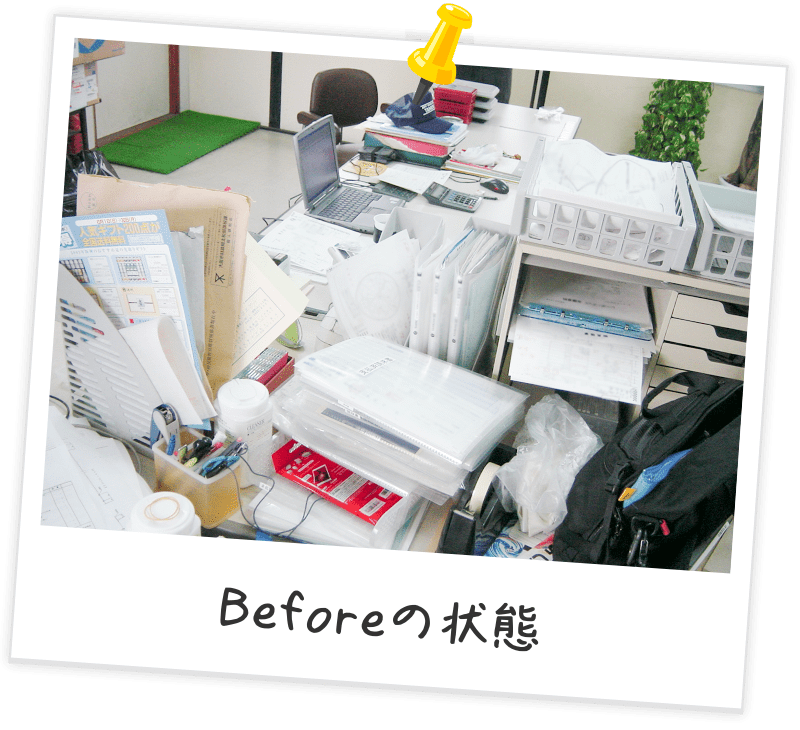
弊社では2005年から3S活動を導入してきました。
3S活動をする前の工場内は色々な物が散乱しており、探す時間や確認する作業に多くの時間を費やしていました。
実施していく中で、要らない物や材料在庫の無駄に気付いていくことが出来ました。
整理・整頓・清掃を行い、出来ていなかったことが見えるようになり、無駄な在庫を減らすことで、業務の効率化に成功しました。
※表はスライドしてご覧いただけます。
比較 | Before | After |
---|---|---|
01 | 壁面に貼った材料の表記は、養生テープで記載していたため分かりにくかった。 | <材料置き場を設置> 落下防止の工夫を行うことで、見た目・安全性を確保。 |
02 | 立て掛けで保管していた材料は、いつ倒れるか分からない状態だった。 | |
03 | 工具がどこに置いてあるか、全員が把握できていなかった。 | <工具を整頓+専用のケースを作成> どこに何があるか明確になり、紛失防止にも繋がった。 |
3S活動の一例
毎月 第1(土)の15時以降は3S活動、第3 (土)15時以降は3Sチーム活動で普段出来ない箇所を中心に行ってます。

人が通る通路を確保し安全管理を徹底
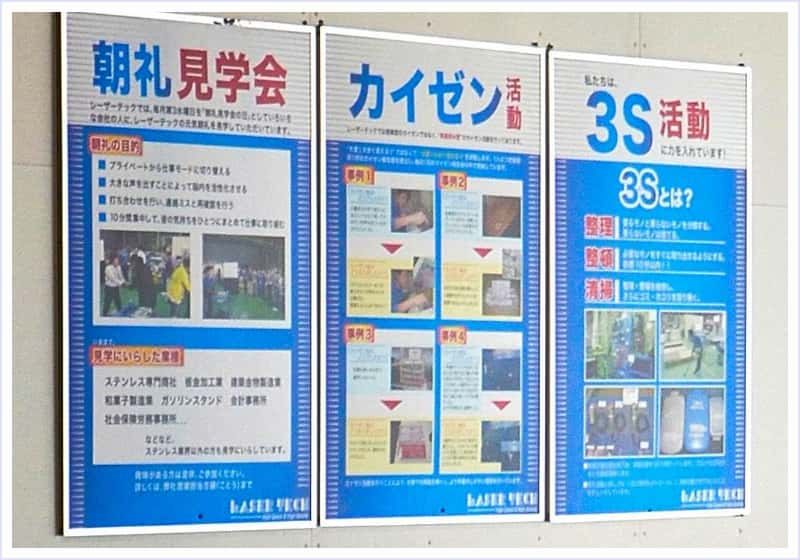
社員一同で徹底した意識改革
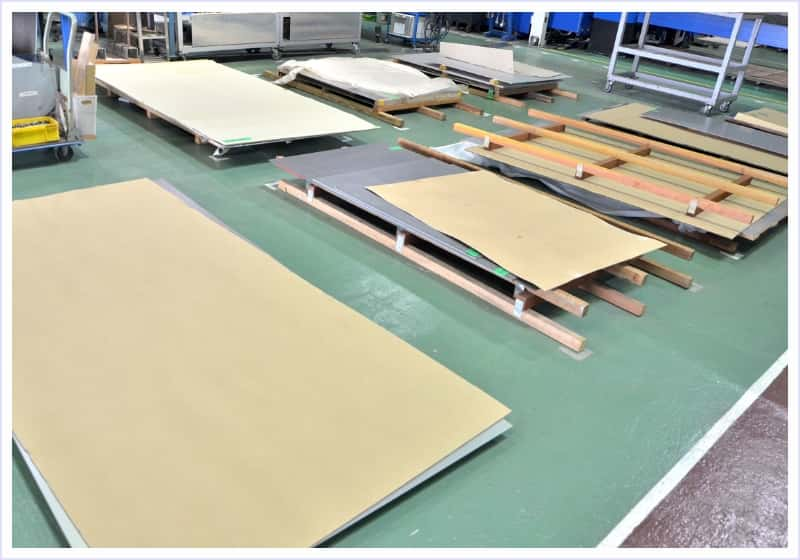
材料を置く場所を専用スペースを確保
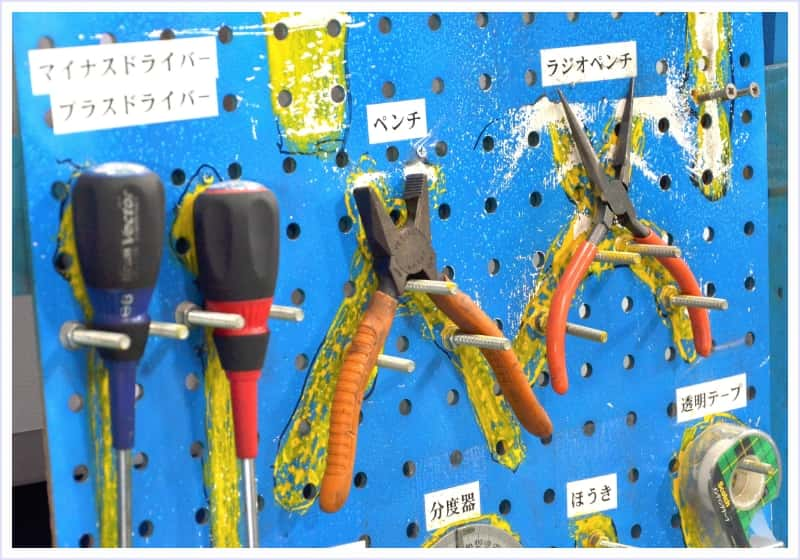
どこに何があるかが一目瞭然。
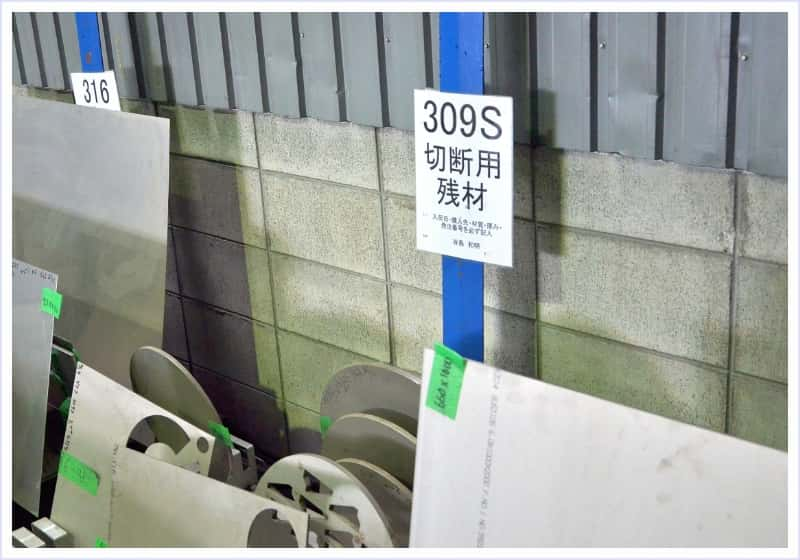
工場の至るところに看板を設置
OPS大阪ものづくり研究会と合同で、日々3S活動に邁進!
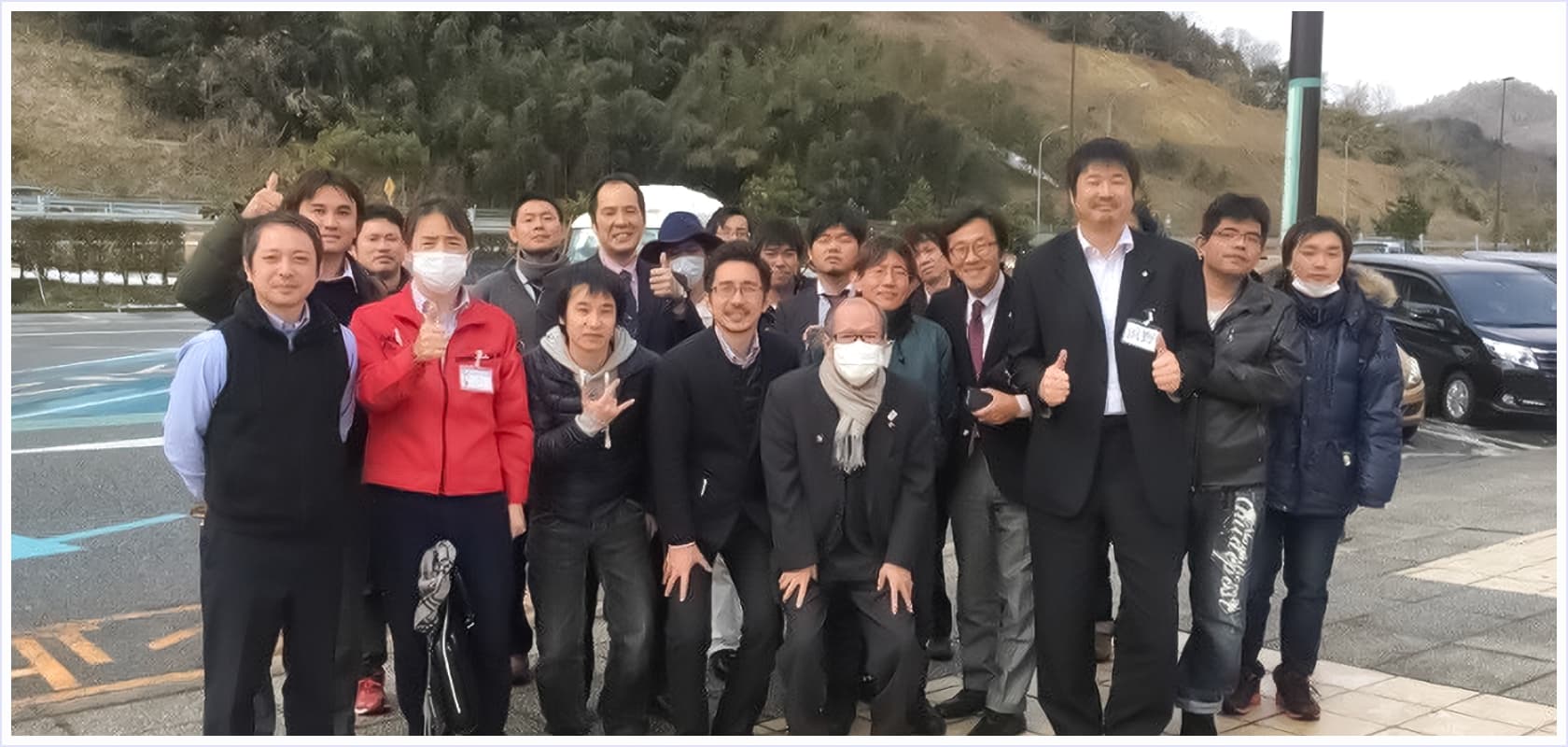
例)OPS大阪ものづくり研究会のご紹介
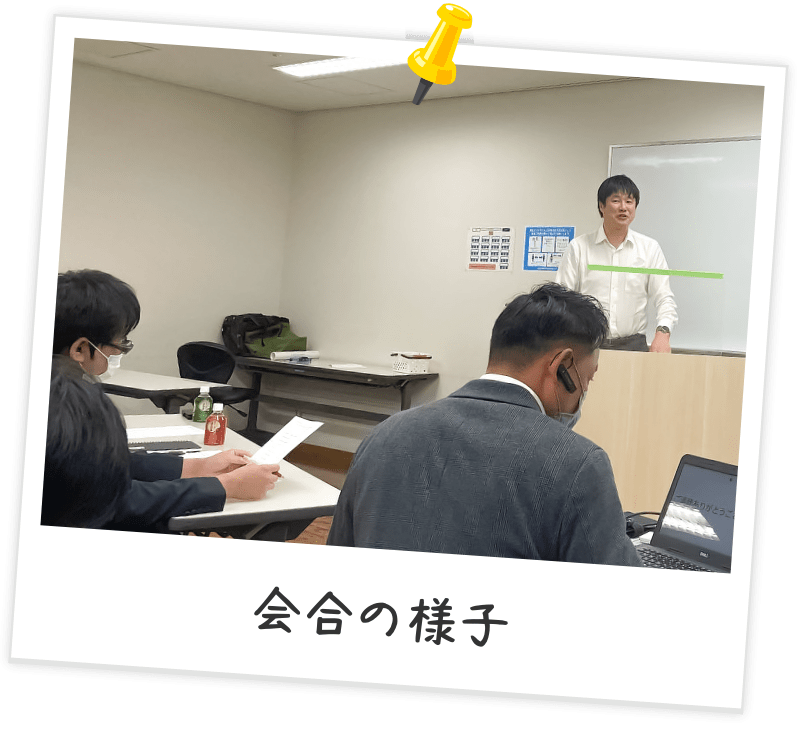
2012年からOPSに入会しました。
月に1度例会があり、他業種の方と共に発表や自社では気付かない問題点を指摘し合っています。
改善の取り組み方や清掃のやり方1つでも違いがあったりと新たな発見が多いです。
これからも力を合わせて活動していきます。
こんなお悩みの方は、ぜひ一緒に活動しませんか?
会社をキレイにしたい方
3Sを通じて社員教育をしたい
効率的な生産を目指している方
他社と交流したい方
いままで、3Sにチャレンジしたが失敗した方